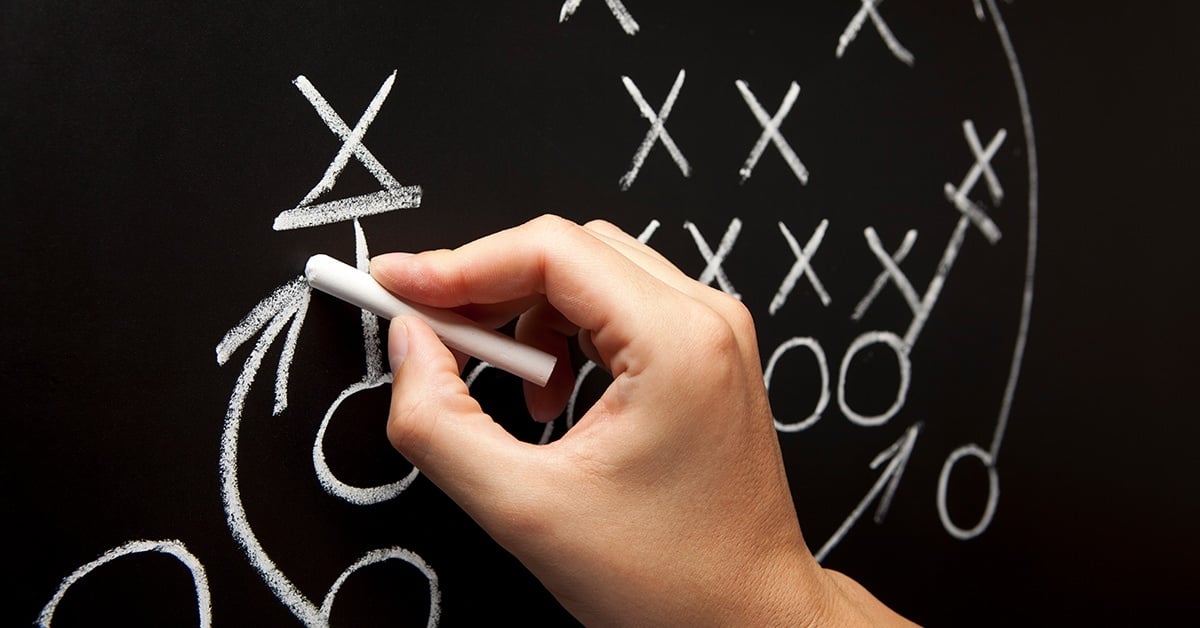
In the life sciences, few words provoke as much anxiety as does “Inspection.” With little notice as to when inspectors will come knocking and no precise understanding as to what they’ll be focusing on, the demands of a TMF inspection can cause even the coolest customer to wilt under the bright lights of scrutiny.
Therefore, it’s understandable as to why the thought of a mock inspection might rub most people the wrong way and remain on the bottom of your corporate to-do list. The stress on staff, the resources required, and the time invested can feel like a drain, considering that you may eventually need to endure a regulatory inspection later.
To help you overcome this resistance, we’ve identified five logic and data-driven reasons as to why holding mock TMF inspections will not only improve your TMF but will make your team a stronger unit, both in terms of regulations and business processes.
Remove Inspection Anxiety
While the EMA has provided its position on what a regulatory inspection should look like, the sheer thought of an inspection is one which can put people on edge. Just think back to your school days; while everyone may have taken the course, the idea of the pressure driven exam scenario caused some folks to panic. The same is true when it comes to TMF inspection—confidence is important for any examination.
One way that confidence is developed, is through practice. As we've learned from clients and industry partners, one of the top employees asks after their first inspection is to have done a dry-run prior to the regulatory review. By building out a true-to-life inspection scenario, it will not only test the team but build their confidence in the real thing.
Develop and Refine an Inspection Playbook
The short time between inspection notification and the actual event is not the time to start preparing the TMF and the team for an inspector’s scrutiny. There’s a reason pro athletes still attend practices. In fact, the reactive behavior will almost certainly cost your organization financially and otherwise. For one, it will eat up a chunk of your resources as they focus solely on the preparation for this inspection, catching up on filing and training, while other priorities—client deliverables, for example—take a backseat. The output of the rushed preparation will most likely result in a number of errors that will speak volumes to the quality system of your organization. Moreover, it will be evident to the inspector that procedures, filing, and training were only updated in the days leading up to the investigation.
A regular series of mock TMF inspections allows your team to run drills and make mistakes in a safe environment, outside the high-pressure scenario of “game-day.” Running these “drills” will provide you the opportunity to pick up on small inspection events and plan for how to handle them and build a culture of "TMF inspection readiness."
Think about the inspector coming in: Where will they sit? Will there be a computer available? Will they have an eTMF account with proper permissions? What training will be required?
Similarly, this exercise will help assign who will “run the plays.” Do you know who will greet inspectors? Who will answer questions? Who is there to provide technical support?
Running mock inspections gives you the opportunity to lay all this out in advance of the real thing and have your team ready to go, with a few surprises as possible.
Identify Training Gaps
A team is an organic cluster of employees, and as such, there is a constant ebb and flow of people coming and going from a company. This is particularly true in clinical research, which has one of the highest turnover rates of any industry, with approximately 20% of all CRO employees changing employers in a given year. IBM noted that turnover, along with “skill leak” due to a lack of practice, amount to a 30% loss of company capabilities per year.
Inspections can happen anytime and turnover isn’t a great explanation when it comes to regulatory issues. With that in mind, it’s important to ensure you’re stress testing the team you have today. Training that occurred last year—or even 6 months ago—might not be relevant today.
Mock inspections can preempt this, and help define inspection roles and responsibilities and are, therefore, vital in identifying where training is required. Mock inspections ensure that when the real inspectors come, you’ve covered your bases ahead of time. An added bonus, to finding training gaps, companies offering comprehensive training ($1500 or more) to their employees are 24% more profitable than those offering less.
Integrate TMF Usage into Daily Life
As we at Montrium believe, TMF usage practices and document integration need to be more holistic. There’s a major industry push for eTMF entry and management to part of the study workflow rather than a document dump after the fact.
With mock inspections adding additional pressure to be inspection ready, it leaves less room to perform TMF “dumps” at an inspection notice. As part of the mock TMF process, the team is continually reminded of the importance of eTMF filing and is regularly evaluated and corrected on their TMF management process.
Along with being ready for inspection (mock or not) at the drop of a hat, this model brings other benefits for the TMF and your team in general. Firstly, this shows to inspectors as a constant flow of quality output, rather than a last-minute scramble. Secondly—and importantly—removing this short-term ramp up required by your team—in particular, the quality team—eases the demands on crucial portions of your workforce and removes error that compounds with rapid-fire review and approvals.
For CROs: Build Sponsor Confidence
At the end of the day, there is a huge amount of responsibility that the sponsor assumes when working with a CRO. The sponsor invests large sums of money in trials and if trials are affected due to critical TMF concerns, it will be their investment lost. Considering that in 2016, the MHRA reported major findings in at least 50% of all inspections, it’s important to remove any doubt that may exist in the mind of the sponsors.
By showing them that your team is prepared—via mock inspections and the reports that result from them—it only builds confidence in the way that your organization manages data. This is a huge value-add during the bid process and when looking to expand your relationship.
Taking Lemons and Making Lemonade
No matter the outcome—positive or negative—mock inspections will lead to tangible reports and lessons learned that can help you proactively plan for inspection day. Mock inspectors will need to document their findings. They shouldn’t hold back; they should note where there were minor and major issues, and they should ask questions about any data gaps and process issues they came across.
Similarly, your team can also document the inspection from their point of view. Were the inspectors able to get TMF access? Was the training sufficient? Where did the inspectors focus? What questions were asked during the inspection?
By taking these two points of view into consideration, a TMF inspection playbook with key roles can be defined and can lead to clearer TMF management. Running a mock inspection is preventative medicine; it may be anxiety provoking, it may not leave a great taste in your mouth but leaves your organization healthier and happier you did it.